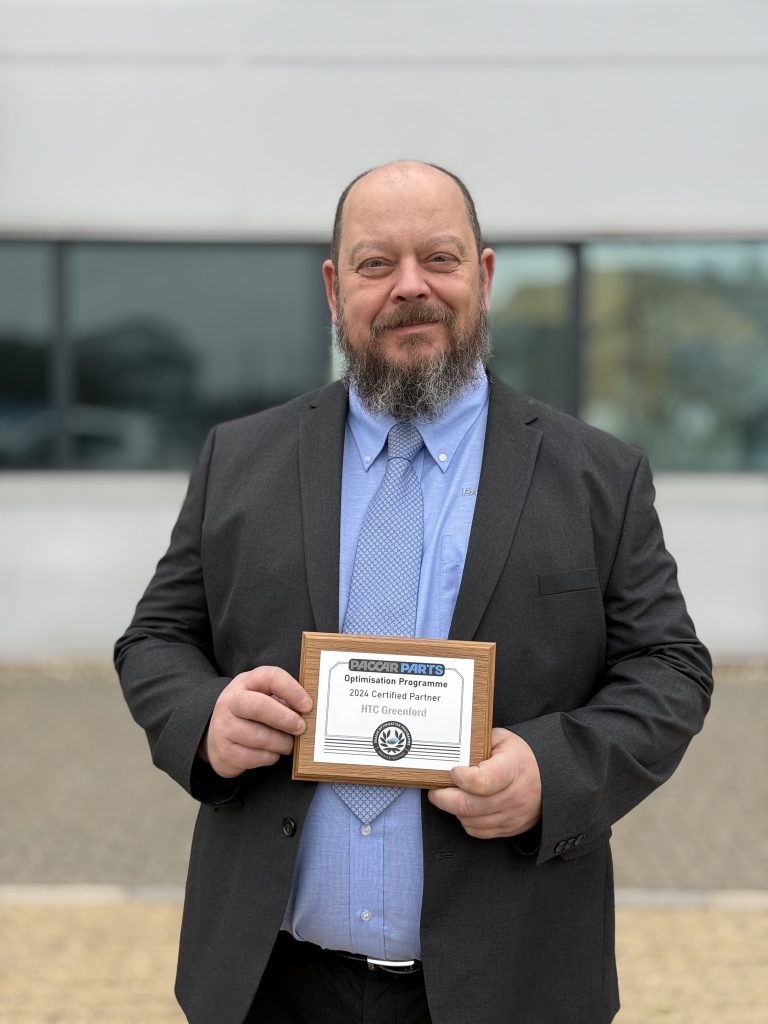
Streamlining Parts Storage and Delivery for Maximum Efficiency and Safety
The team at HTC Greenford has reached a significant milestone with the completion of the Paccar Parts Dealer Optimisation Programme, an achievement that sets a new standard in efficient parts storage, delivery, and workplace organisation. This milestone was marked by a tour of the newly optimised parts department, led by Parts Manager Don Cairns, and a ceremony to award the team for their hard work and dedication.
A Transformative Journey
HTC Greenford’s journey through the Dealer Optimisation Programme was unique, given its recent relocation from Park Royal to a spacious, purpose-designed site. However, this transition presented challenges, as the team had to maintain operations, move thousands of parts, and work through the optimisation programme simultaneously.
Despite these hurdles, the results speak volumes. The new layout ensures a safe, stress-free, and efficient environment for staff while prioritising customer experience and vehicle uptime.
Steve Foster, Parts Director, highlighted the positive impact of the new site:
“The extra space is a luxury we didn’t have before. Allocating specific areas for parts and equipment has been a game-changer for both efficiency and safety.”
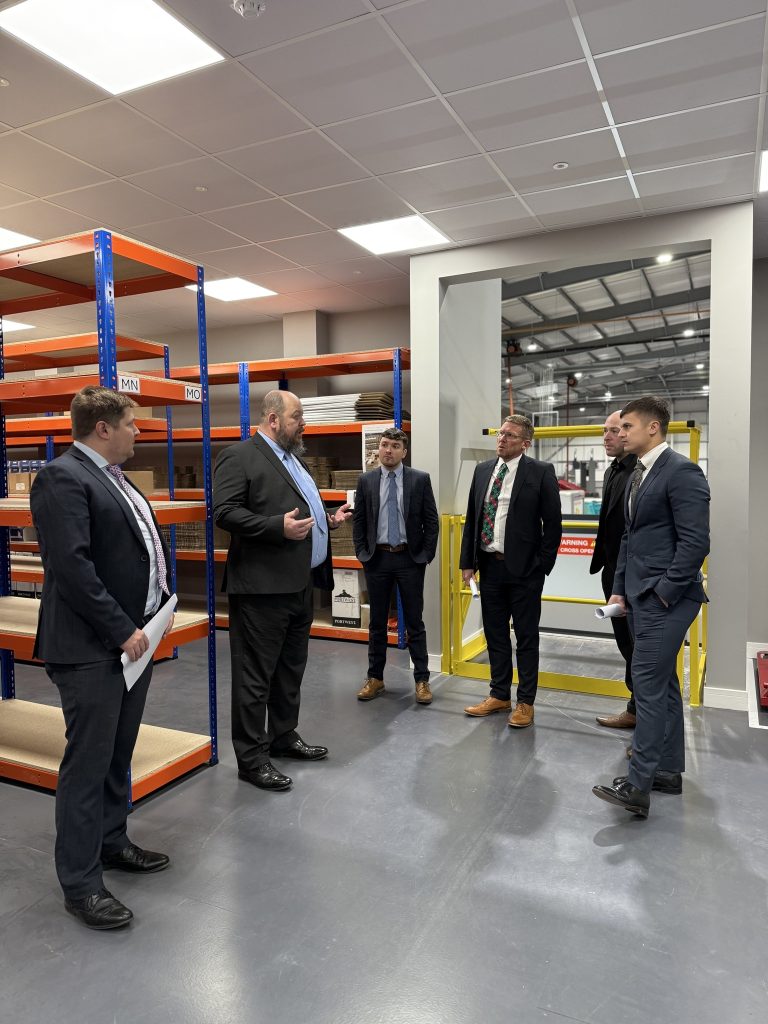
Key Improvements
1. Strategic Layout & Gold Zone
– The optimisation programme introduced the “Gold Zone”—a dedicated area for the most frequently used parts.
– This ensures quick and easy access for technicians, delivery teams, and walk-in customers, significantly reducing downtime.
Eddie Holden, Continuous Improvement Facilitator at Paccar Parts, likened this to a car park with grid lines:
“Without an organised system, locating parts can be chaotic. Now, everything has a designated spot, which makes retrieval seamless.”
2. Increased Storage Density
– Shelving systems were re-evaluated, increasing from five levels to eight in some areas.
– This allows for more parts to be stored in a smaller footprint, maximising space without compromising accessibility.
3. Pallet Integration
– Pallet runs were incorporated into the design, enabling safe and efficient unloading of large items like batteries directly from trucks.
– Steve Foster noted this as a priority during planning, and the results have exceeded expectations.
4. Data-Driven Decisions
– Quarterly reviews now reassess which parts belong in the Gold Zone, adapting storage to meet changing demands.
– Every decision is backed by data to ensure ongoing efficiency.
The Human Element
The programme’s success wouldn’t have been possible without the dedication of HTC Greenford’s team. Don Cairns, Parts Manager, reflected on the hard work involved:
“It was challenging, but the benefits are colossal. Our team now has a smarter, safer, and more efficient workspace that supports both staff and customers.”
Team members echoed this sentiment, emphasising how the changes have made their daily tasks smoother and more manageable.
Celebrating Success
The day concluded with a plaque presentation to Don Cairns, awarded by Eddie Holden, as a recognition of HTC Greenford’s achievements. Attendees, including leaders from Paccar Parts and HTC, celebrated this milestone and discussed opportunities to share the programme’s learnings across other sites in the network.
A Bright Future for HTC Greenford
HTC Greenford’s optimised parts department is a testament to what can be achieved with proper planning, dedication, and teamwork. With plenty of room for future growth and a robust system in place, the site is positioned to maintain its exceptional standards for years to come.
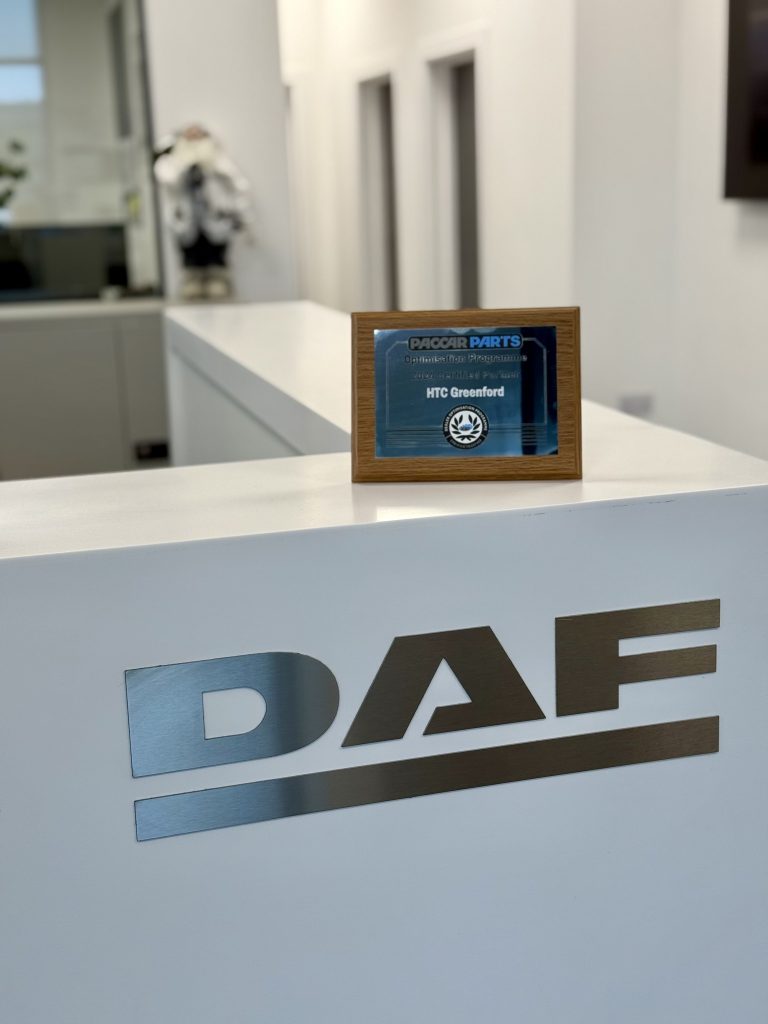
Don Cairns summed it up best:
“This is just the beginning. By maintaining these systems and continually improving, we’ll ensure HTC Greenford remains a model of efficiency and customer service.”
Congratulations to HTC Greenford on this outstanding achievement!